Mirrors play a significant role in everyday life, but many may not realize the importance of their reflective coating.
The primary reason mirrors are coated with silver is its exceptional ability to reflect light, often achieving up to 95% reflection across the visible spectrum. This quality is essential for creating clear and bright images.
While silver is commonly used in high-quality mirrors, other metals like aluminum are also options.
In household mirrors, silver is preferred because it produces a more appealing reflection. The process of applying this silver coating involves treating glass with silver-ammonia compounds, resulting in a durable and reflective surface.
Understanding why silver is favored for mirror coatings can enhance appreciation for these everyday objects. From personal grooming to decorative purposes, mirrors are more than just glass; they are a reflection of scientific principles at work.
The Science of Silvering and Reflectivity
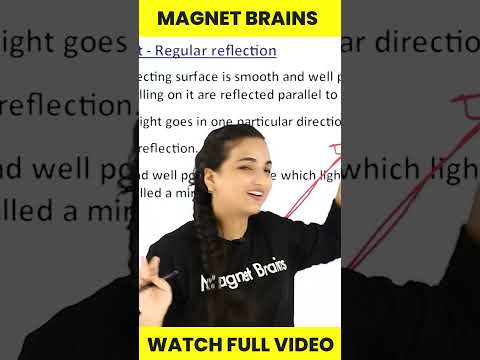
The process of silvering is essential for creating effective mirrors. Silver coatings enhance reflectivity, allowing mirrors to efficiently reflect light across various wavelengths.
This section explores the fundamentals of silvering, compares different mirror coatings, and highlights advances in silvering technology.
Understanding Silver Coating and Reflectivity
Silvering involves applying a thin layer of silver to a substrate, typically glass. This layer transforms a plain surface into a highly reflective mirror. The silver coating achieves high reflectivity, especially in the visible spectrum.
The process relies on careful control of thickness and smoothness to minimize imperfections.
Silver has low emissivity, meaning it reflects more light and absorbs less. This property is essential for applications where clarity and brightness are crucial, such as in optical instruments.
Comparative Analysis of Mirror Coatings
While silver is a popular choice for mirror coatings, there are alternatives like aluminum. Each material has distinct characteristics affecting performance.
Silver mirrors excel in the visible and near-infrared ranges, making them ideal for telescopes and scientific instruments.
Aluminum, while slightly less reflective, is more durable and resistant to tarnishing. This longevity makes aluminum a practical option for many applications. The choice between silver and aluminum often depends on the specific use, such as needing high reflectivity or robustness.
Advances in Silvering Technology
Recent developments in silvering techniques have improved the process’s efficiency and results.
Innovations include vacuum deposition methods that apply silver in controlled environments. This technique allows for better adherence and uniform coatings.
Additionally, the ability to control the angle of incidence during application enhances the quality of reflection. These advancements result in mirrors with superior performance for various applications, including high-end optical mirrors and specialized devices in scientific research.
Application and Durability of Mirror Coatings
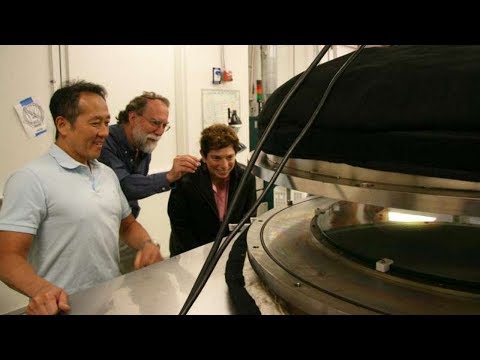
Mirror coatings play a crucial role in enhancing reflective properties and ensuring longevity. Different materials offer unique durability profiles and applications, making it important to understand their characteristics.
Durability Factors in Silver Mirrors
Silver mirrors are known for their excellent reflectivity. However, they can tarnish over time due to exposure to air and moisture.
To combat this, many manufacturers use a protective layer over the silver coating. This protected silver is more resistant to oxidation and retains its reflective qualities longer.
Additionally, silver’s noble metal status means it provides high performance in optical instruments. Yet, for environments with high humidity or varying temperatures, alternatives like protected aluminum are preferred due to their better durability.
Applications of High Reflectivity Mirrors
Silver-coated mirrors are widely used in various optical applications. Their ability to reflect light makes them ideal for telescopes, which require high clarity and precision.
In addition, they are utilized in scientific instruments where accurate light reflection is paramount. High reflectivity mirrors enhance the efficiency of systems like lasers and optical devices.
Silver mirrors are an affordable alternative for many applications; however, their maintenance can be more demanding compared to other materials.
Alternatives to Silver and Future Trends
While silver remains a popular choice, researchers are exploring alternative coatings.
Gold plating, for instance, offers excellent performance in the near-infrared (NIR) and infrared (IR) regions, making it suitable for specialized applications.
Dielectric layers are another trend, providing advanced reflective coatings without the drawbacks of metal plating. These layers can protect against environmental factors while maintaining high reflectivity.
As technology advances, the market may see a shift towards more durable and efficient options, ensuring optimal performance across various optical applications, including telescope mirrors.
The ongoing development in mirror coatings, including methods like mercury silvering, highlights the industry’s focus on improving both durability and functionality.