The clear aperture of an optic is a crucial aspect that affects how light interacts with an optical component.
It refers to the diameter or size of the area within an optical system that allows light to pass through and meet the required specifications.
Understanding the clear aperture helps in evaluating the performance and efficiency of lenses and other optical devices.
In an optical system, the clear aperture plays a significant role in determining how much light can be gathered and transmitted. If the clear aperture is smaller than the actual size of the optical component, it can limit light throughput and impact image quality.
This limitation is often due to manufacturing constraints, which makes it essential for designers and engineers to account for it during the development process.
By grasping the concept of clear aperture, readers will appreciate its importance in both everyday optical devices and advanced systems used in various applications. This foundational knowledge opens the door to exploring more complex topics within optics and contributes to a deeper understanding of how these systems function.
Fundamentals of Clear Aperture
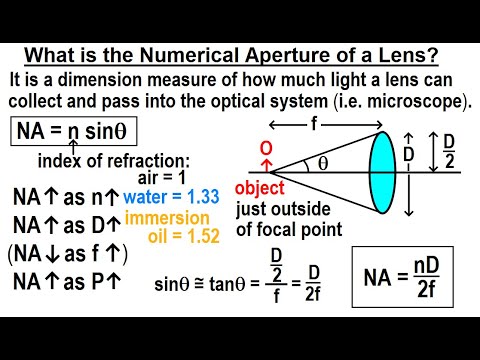
Clear aperture plays a critical role in defining how an optical component performs. Understanding its definition and standard measurements is essential for anyone working with lenses and other optical devices.
Definition and Importance
Clear aperture refers to the area of an optical component that can effectively transmit light without interference. It is crucial because it directly impacts the optical performance of lenses and other elements.
The clear aperture is usually defined by the diameter of the lens or the dimensions of the optical area that meets specific quality standards.
Optical performance outside this area may not meet the required specifications. This often means that any light paths not within the clear aperture can produce distortion or loss of image quality.
Identifying this area allows manufacturers and users to evaluate how well a component will perform under different wavelengths of light. Understanding clear aperture helps ensure precision quality in optical design.
Standard Measurements
Standard measurements of clear aperture often correspond to the specific diameter of lenses or optical components.
For many lenses, the clear aperture should be at least 90% of the lens diameter. This measurement ensures that most of the transmitted light passes through the desired region.
Manufacturers usually specify the clear aperture alongside surface accuracy and optical coatings. This information helps users select the right components based on their applications.
In high-precision optics, a larger clear aperture may be necessary to capture more light and achieve better resolution. Knowing these standards allows for better performance in various applications, from cameras to scientific instruments.
Factors Influencing Clear Aperture

Several factors play a critical role in determining the clear aperture of an optical component. These factors include manufacturing tolerances, surface quality, and the coatings applied to the surface. Each aspect directly impacts the optical performance and usability in various applications.
Manufacturing Tolerances
Manufacturing tolerances refer to the allowable deviations from specified dimensions during the production of optical components. These tolerances can affect the clear aperture significantly.
If the mechanical tolerance is too loose, the final product may not meet required specifications.
For example, when a lens is produced, there may be acceptable variations in size that can either decrease or increase the clear aperture. Additionally, due to manufacturing constraints, it is often impossible to achieve a clear aperture that is exactly equal to the lens’s overall diameter.
Many manufacturers specify a clear aperture as a percentage of the total size, which helps users understand what to expect in terms of optical performance.
Surface Quality and Accuracy
Surface quality and accuracy play a crucial role in defining the clear aperture. If the lens surface is rough or not accurately shaped, it can lead to light scattering and loss of clarity.
Surface roughness affects how light interacts with the optic, particularly at different wavelengths of light.
For an optical system to operate effectively, the surface must be polished to achieve the required precision. The higher the surface accuracy, the better the optical performance.
Manufacturers frequently test these surfaces to ensure they meet the necessary specifications. A lens in a high-quality telescope or microscope may need extremely smooth surfaces to deliver clear imaging.
Optical Coatings
Optical coatings are applied to enhance the performance of lenses and other optical components. These coatings are crucial for minimizing light reflection and maximizing transmission.
Different coatings can alter the interaction between the light and the clear aperture.
For instance, anti-reflective coatings improve the clear aperture’s ability to transmit light without interference. Without proper coatings, light loss can occur, leading to dimmer images.
In applications like microscopes, where clarity is paramount, coatings become essential. They ensure that the clear aperture effectively utilizes the incoming light for clearer, more vibrant images.
Testing and Verification

Testing and verification of the clear aperture in optical components are crucial in ensuring their performance and quality. This process often employs sophisticated techniques to analyze optical surfaces and assess their specifications accurately.
Interferometry in Practice
Interferometry is a key method for measuring optical surfaces. This technique uses an interferometer to create an interference pattern, known as fringes. These fringes indicate any deviations in the surface shape, allowing for precise measurements of the clear aperture.
By analyzing the fringe pattern, technicians can detect surface errors down to the nanometer level. The root mean squared (RMS) value is commonly used to quantify these deviations.
A lower RMS value usually indicates a smoother surface, which is vital for optical performance. Effective use of interferometers ensures that the clear aperture meets the required specifications, ultimately preserving the integrity of the optical system.
Assessing Surface Quality
Surface quality assessment is critical in determining the functionality of the clear aperture. Techniques such as microscopic examination can reveal details about surface roughness, which affects light transmission and overall performance.
A common metric for evaluating surface quality is the average roughness (Ra) measurement. This parameter complements RMS values in providing a complete picture of surface character.
In an optical context, a rough surface can scatter light, impairing image clarity. Therefore, manufacturers aim for optimal surface conditions, often striving for an Ra value in the sub-micrometer range. Maintaining high surface quality ensures that the optical component functions as intended within its application.
Design and Application Considerations

In designing optical systems, understanding the clear aperture is crucial. This section focuses on the principles guiding optical design and strategies for optimizing performance. Both aspects play a vital role in achieving precision quality in optics.
Optical Design Principles
Optical design takes into account several key factors, including the focal length and radius of curvature.
The clear aperture defines the usable area of a lens or mirror, impacting how light enters and exits the optical system.
Concern for surface form is essential. A polished surface minimizes light loss and aberrations. An optical designer must also consider potential wedge effects, which can distort images if the surfaces are not parallel.
The clear aperture directly affects the system’s performance and determines its ability to gather light effectively. Adhering to strict specifications during optical fabrication ensures that components meet design requirements, which helps in achieving optimal performance.
Performance Optimization
To optimize optical performance, precise measurement of the clear aperture is essential.
This includes assessing the surface accuracy and ensuring it meets design specifications.
Factors like the type of coating also influence performance, impacting reflection and transmission rates.
Using simulation software can aid in visualizing the effects of different design choices.
By adjusting the radius of curvature and examining the impact of surface imperfections, designers can refine the optical system.
Regular testing during the fabrication process helps identify potential issues early.
Ensuring the clear aperture meets specifications is vital in producing high-quality optics that perform well in real-world applications.